Saving green by building green
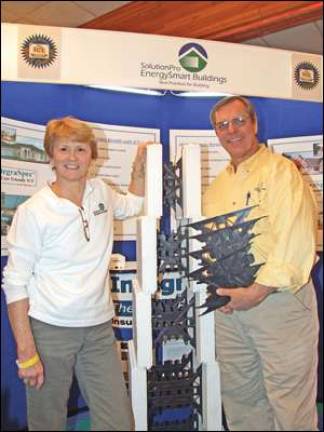
MILFORD – Insulated concrete forms are described as Legos for big kids. No matter how elementary that sounds, the benefits of this new type of home and commercial construction can translate to tremendous savings for both contractor and consumer, not to mention the environment. Despite having been used throughout the world for decades, insulated concrete forms (ICFs) are making their first appearance in Pike County. Last year, one out of six houses in the United States was made with this system. Essentially, ICF houses use a permanent Styrofoam mold which is filled with cement to create the exterior walls. The expanded polystyrene foam mold acts as an insulator and can yield over an R-40 insulating value, compared with a wood frames typical R-19. Dave Farrington and Carrie Thomas of Shohola wanted to try something new and different. Interested in construction, and wanting to get involved in the ground floor of the green building movement, they started Solution Pro Energy Smart Buildings and displayed this up-and-coming product at the Pike County Builders Associations Home Show last weekend. The company provides many products necessary in green construction, but is primarily centered around ICFs. The husband and wife team spent about 18 months researching the concept, interviewing 15 different ICF providers before choosing to market this product in 2003. The Styrofoam material is both made from recyclable materials and can be recycled itself. It is lightweight, and since it is manufactured in Massachusetts, it can be transported very efficiently – a large component to green building. They explained that concrete homes with this new type of insulation provide a thermal envelope for the home which will lessen heating and cooling costs, virtually eliminating mold and mildew. It has no off-gasing, creates an effective sound-barrier, and improves the quality of the air within the home. Additional benefits come with increased fire ratings and protection against wind and flood damage. These benefits also extend to the builder. Thomas explained that construction sites are safer and cleaner because of this new material, and that builders can finish faster. The only tool you really need to construct a home with this material is a handsaw. Farrington said the system is very versatile. There is literally nothing you cant achieve with this. The actual façade of the house can be like any other conventional home. Further, waste is drastically lessened and the left over materials can be recycled. The government also gives a $2,000 tax credit per house for builders who meet a certain energy efficiency, which ICFs provide. According to the Portland Cement Association, houses built with exterior cement walls will consume an estimated 44% less energy to heat and 32% less energy to cool. In an average 2,000-square-foot home in the United States, that means upwards of $200 in annual energy savings, and hundreds more in equipment savings because of the decreased need for larger heaters or air conditioners. Its positive for the environment. Its positive for the homeowner, and its very positive for the builder, Thomas asserted. Change in an industry is hard to achieve, acknowledged Farrington, who also stated that the transition for builders to go from something they have been doing for decades to this new means of construction is a challenge.